Injector needle valve parts due to long-term high temperature and pressure in the harsh conditions of work, often back needle stuck in the valve body failure, even serious and even scrapped. Even if the couple can be repaired, but also time-consuming effort, but also can not fully guarantee the quality of their work after the repair. Experienced hands and maintenance personnel in the production of practice summed up five small experience, you can effectively prevent the needle valve is sintered and stuck. (1) In the maintenance of the injector, all parts should be carefully cleaned after decomposition. Do not just clean the needle and valve parts, while the pressure regulating spring, spring nut, adjusting screw and tappet and other parts regardless of. If these parts of the adhesion of pollutants can not be cleared, will be tapped to the top of the needle through the tappet, fleeing needle movement between needle and needle valve needle stuck. (2) Can not remove the oil return pipe. The oil return pipe will drain the diesel oil leaked from the needle valve and the valve body to the low-pressure oil circuit at work, thus avoiding the waste and ensuring the cleanliness of the fuel. If the oil return pipe is removed, not only the oozed diesel can not be reutilized, but also the dust particles in the air will enter the oil injector through the connection hole of the oil return pipe and the injector so as to easily cause the needle valve to be stuck. Some people in the removal of the oil return pipe on the injector hole blocked, this method is even more undesirable. Because when the needle valve leakage of diesel fuel overflow from the upper chamber, the hydraulic pressure is not short, eventually leading to the needle valve parts can not work, and are sintered together. (3) after the engine is installed to install high-pressure tubing, said the first low-pressure oil circuit connected, then the high-pressure tubing connected to the fuel pump, and then set the throttle handle at the maximum fuel supply position, swivel crankshaft, fuel injection pump , Until the high-pressure tubing 5-10 times after the oil-side injection, and then the high-pressure tubing out the fuel injector and connected. In doing so, can be stored in the high-pressure tubing and fuel pump out of the joint on the sewage out of the dirt to prevent dirt with high pressure oil into the injector and the needle stuck. (4) When both ends of the high-pressure tubing and the fuel injection pump and injector necklaces are spilled, the method of plugging lead wire, asbestos wire, etc. can not be adopted to implement plugging. Available thin copper skin cut into the corresponding size of the round pad, punch a hole in the middle of the pad, pad at the high-pressure hose connector. Because lead wire and asbestos wire is easily squeezed into pieces, with the high-pressure tubing into the fuel injector, causing the needle stuck. (5) Some diesel engines are equipped with a needle filter at the oil outlet of the high-pressure fuel pipe. The filter works well in the magazine of diesel oil. It is quite wrong for someone to remove the fuel injector while it is being installed. The green heart should not be removed not only installed, but also should be cleaned regularly.
Thermal Spray Materials
Metals, alloys and composite powders commonly used in thermal
spray hardfacing technology and coating service. These unique powders are
instantly heated by thermal spraying (welding) methods such as high temperature
flame or explosive flame, and are sprayed and deposited on the cold or hot
workpiece surface with high-speed heat flow in a molten or semi-melted state to
form a surface Reinforcing layer, in order to improve the wear resistance,
corrosion resistance, heat resistance, oxidation resistance or repair of
external dimensions of the workpiece surface. XTC produces WC, CrC, Oxide
Ceramic, Boride Powder, Metal Alloy Powder, Pure Metal and Spray Wire, etc.
product. For HVOF/HVAF/plasma/Flame spray coating and applications. Meet the
wear and corrosion resistance requirements of different surfaces.
WC, CrC oxide ceramic powder and boride
products are excellent in wear resistance and high temperature corrosion
resistance. Taking WC products as an example, the hardness can reach
HV1300-1500, and the temperature of CrC products can reach 800 degrees Celsius.
Metal alloy powder, Pure Metal and Spray
Wire products have more applications in glass mold, steel and machinery
industries. And XTC products are now become more and more popular in Metal
spray coating and thermal spray coating industry.
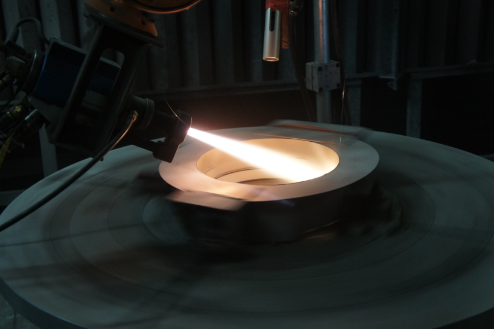
Coating Service,Metal Spray Coating,Flame Spray Coating,Thermal Spray Coating
Luoyang Golden Egret Geotools Co., Ltd , https://www.xtclasercladding.com